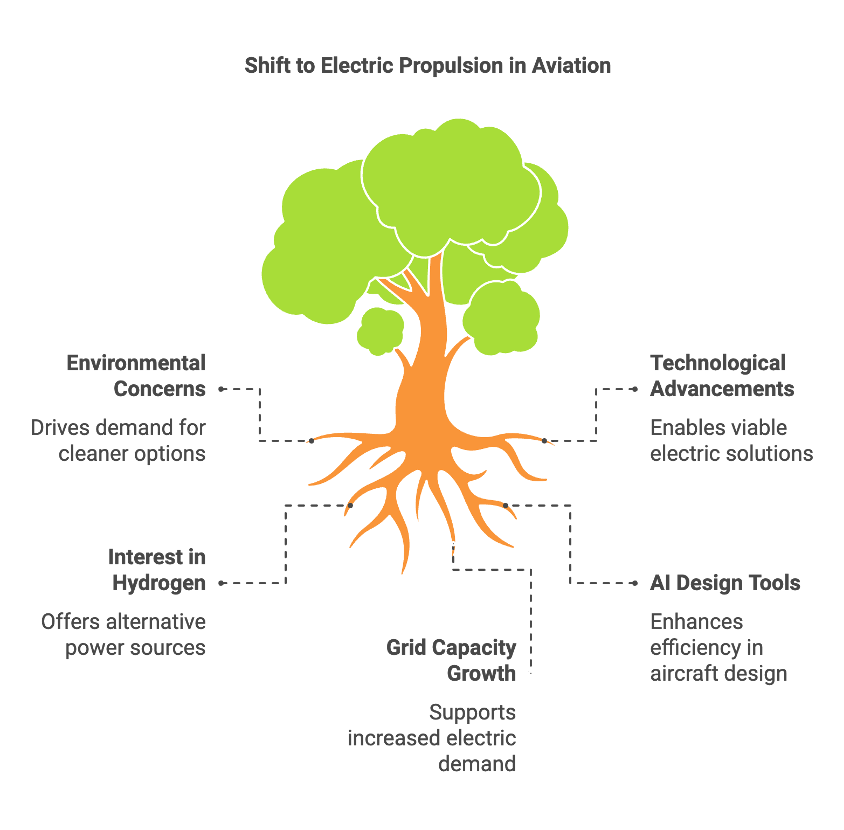
Over the next ten years, the commercial aviation industry is poised to undergo a transformative shift from traditional hydrocarbon-based propulsion toward electric propulsion. This change to electric commercial aviation is being driven by several key factors: environmental concerns related to greenhouse gas emissions, technological advancements in battery energy storage, rising interest in the use of hydrogen as an onboard power source, and the emergence of sophisticated artificial intelligence (AI) design tools that streamline aircraft design. Coupled with expected growth in the capacity of the U.S. electrical grid, these drivers make a strong case that the aviation sector is on the cusp of an electric revolution.
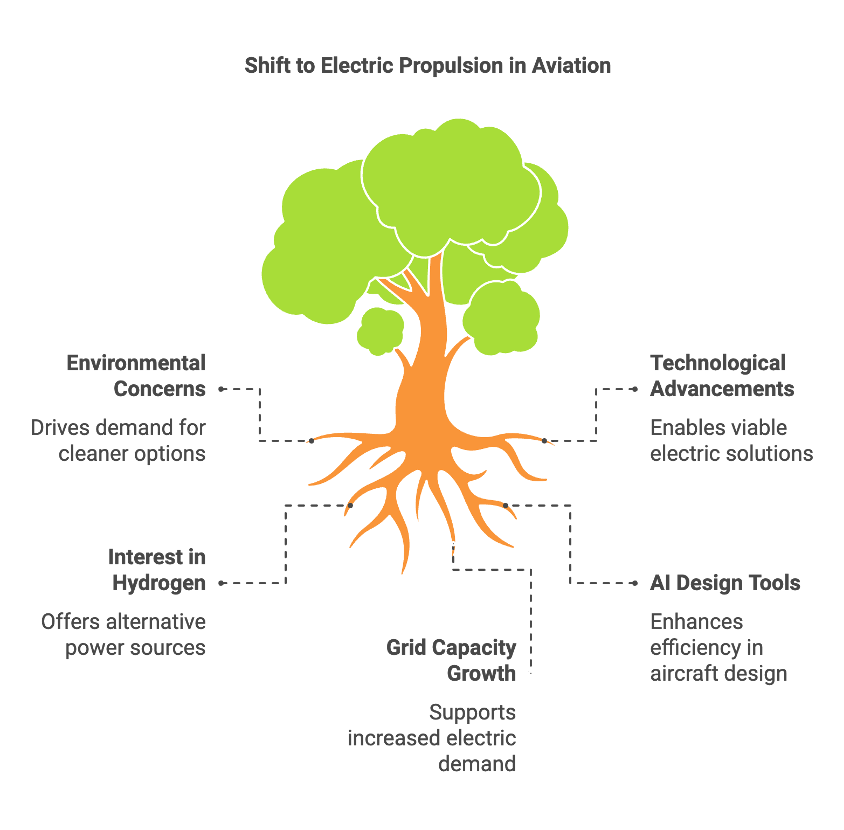
We will explore the reasons for this shift, outline the methods by which electric aviation technology can and will be developed, and discuss the stages by which commercial aviation will likely incorporate electric propulsion into its mainstream operations. Technical analysis—particularly surrounding battery technology, AI-assisted design, and alternative onboard power generation—will aim to speak to a wide audience while providing enough detail for those familiar with scientific and engineering concepts.
Reasons for Shifting to Electric Propulsion
Economic Incentives
Economic incentives will play a pivotal role in driving the adoption of electric propulsion across the commercial aviation sector. By leveraging highly efficient electric motors and advanced battery systems, and lower-cost components, commercial operators of electric aircraft can significantly cut operational costs related to fuel, maintenance, and engine overhauls. Unlike traditional jet engines that require frequent inspections due to high-temperature turbine operations, electric propulsion systems generally experience less wear and tear, translating to lower maintenance outlays. The simplicity of the electric powertrain in the reduced number of moving parts also plays a big role in reducing costs. Additionally, using CFD methods to optimize exterior design to enhance aerodynamic efficiency will further improve range and reduce energy consumption, improving operating margins for the operators. Over time, these cost-savings will lead to higher profit margins for commercial operators, making electric propulsion not only an environmentally responsible choice but also a money-making business strategy.
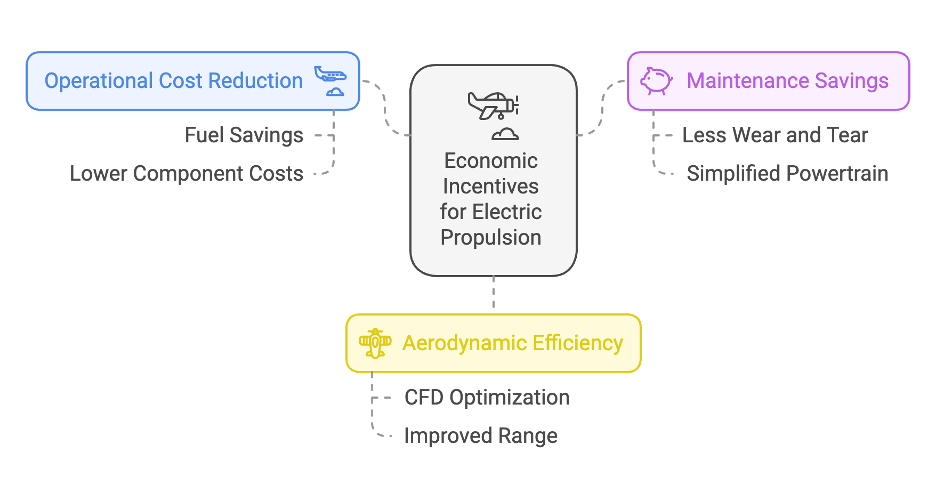
Environmental Incentives
The most pressing motivation behind electric aviation is the urgent need to cut carbon emissions. The Intergovernmental Panel on Climate Change (IPCC) has stressed the critical role of the transportation sector in contributing to greenhouse gases, with aviation accounting for a significant share of these emissions. Transitioning to electric propulsion lowers the reliance on jet fuel, which in turn reduces CO₂ emissions and other pollutants like nitrogen oxides (NOₓ) and particulate matter.
Regulatory Pressures and Policy Changes
Governments across the globe are implementing regulations that limit allowable emissions. In particular, the European Union has signaled stringent targets for aviation-related carbon emissions under its “Fit for 55” proposal. The United States is also evaluating measures to incentivize sustainable aviation fuels (SAFs) and advanced propulsion systems. These regulations will push manufacturers and airlines to pursue low- or zero-emission aircraft solutions—chief among them, electric or hybrid-electric flight technologies.
Public and Market Demand
Society’s growing commitment to greener practices is generating heightened interest in eco-friendly travel. Airlines that can demonstrate tangible reductions in their carbon footprint often gain a competitive edge in the market. Furthermore, a significant segment of travelers is increasingly aware of their environmental impact. By offering electric flights, airlines position themselves as eco-conscious, attracting customers seeking to minimize their travel-related emissions.
Advancements in Battery Technology
Current Battery Landscape
Modern electric aircraft rely on high-capacity batteries to store and deliver electrical energy to the propulsion system. At present, lithium-ion (Li-ion) batteries dominate electric aviation prototypes because of their favorable energy density (typically in the range of 250 to 300 Wh/kg). However, for larger commercial applications, even these advanced Li-ion batteries pose limitations related to weight, charging time, and lifecycle.
Future Battery Chemistries
The electric aviation industry is shifting its gaze toward emerging battery technologies that promise higher energy densities. These include:
- Solid-State Batteries: By replacing the liquid electrolyte with a solid material (e.g., ceramic or glass), these batteries can potentially boost the energy density to over 400 Wh/kg while enhancing safety. A solid electrolyte reduces the risk of thermal runaway, thereby improving battery stability.
- Lithium-Sulfur (Li-S) Batteries: Lithium-sulfur chemistry can theoretically achieve energy densities up to 500 Wh/kg or more. While issues such as poor cycle life and low conductivity remain challenges, significant research investment could lead to Li-S batteries that are commercially viable within the next decade.
- Lithium-Air (Li-Air) Batteries: Though still largely in the research phase, lithium-air batteries have an even greater theoretical energy density (potentially exceeding 1,000 Wh/kg). Achieving stable and cost-effective Li-air cells may be one of the most significant breakthroughs for truly long-haul electric flight.
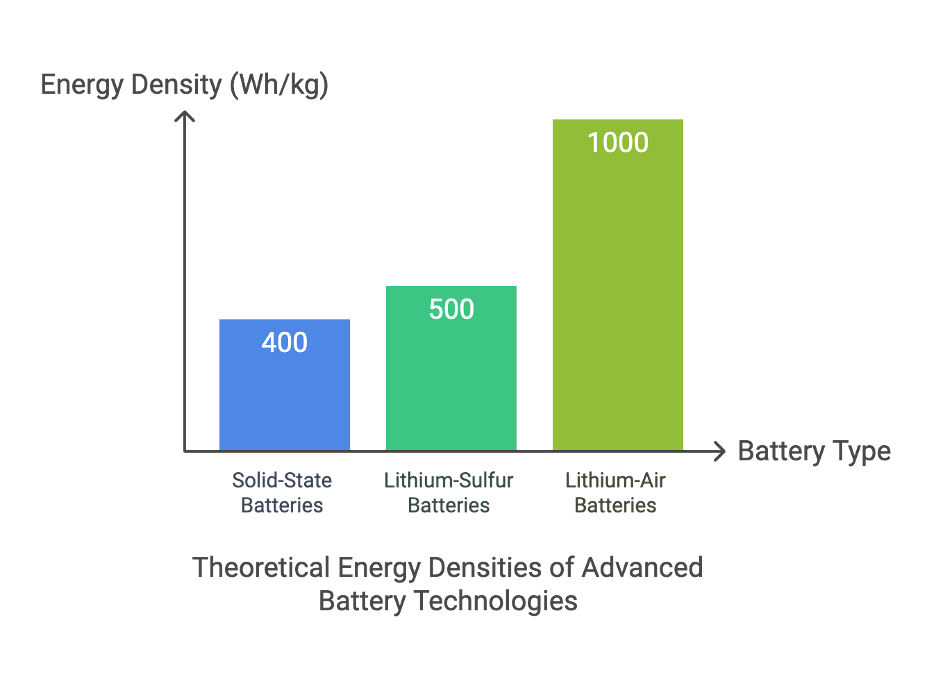
Given current rates of technological progress, it is realistic to anticipate that by 2034, commercial electric aircraft will be able to operate regional routes of up to 600 to 1,000 miles—possibly more—using high-performance lithium-based or solid-state batteries.
Battery Manufacturing and Cost
To meet aviation’s needs, large-scale battery manufacturing will have to ramp up dramatically, improving economies of scale. Companies are likely to rely on “gigafactories” designed specifically for advanced battery production. In tandem, research funding from public and private institutions should speed up development of new battery chemistries. These improvements in production volume and technology will likely help drive down costs, making battery-powered aircraft more economically viable.
AI-Driven Design Tools for Electric Aircraft
The Role of AI in Design
Artificial intelligence and machine learning algorithms are revolutionizing the aircraft design process. Instead of relying solely on classical computational fluid dynamics (CFD) simulations, engineers now integrate AI-driven models that can explore thousands or even millions of potential design variations rapidly. Neural networks can “learn” from existing data and predict how certain design choices—like fuselage shape, wing geometry, or battery placement—will affect aircraft performance.
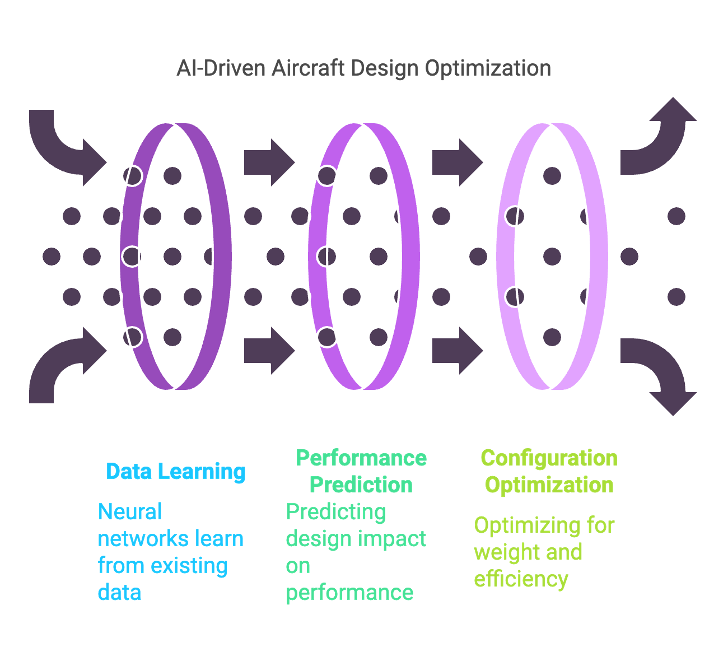
By leveraging AI-assisted methods, companies can optimize configurations for weight distribution, aerodynamic efficiency, and energy consumption. This helps tailor designs more precisely to the unique constraints of electric propulsion, where energy capacity (Wh/kg) and power output (kW) are critical factors for flight duration and payload capacity.
Accelerated Prototyping and Testing
Another significant advantage of AI is the ability to conduct virtual stress tests and flight simulations at scale. Engineers use advanced simulation environments to subject digital prototypes to thousands of flight conditions, weather scenarios, and mechanical stress situations. AI can analyze performance in real time, providing insight into which structural components may be optimized or replaced with lighter materials.
Consequently, the timeframe for prototype creation and testing can be shortened considerably. What once required years in a wind tunnel or months in iterative prototyping can now be accomplished far more efficiently. This accelerated process is vital to meeting the tight timelines envisioned for electric aviation’s emergence.
U.S. Electrical Grid Growth Projections
Increasing Demand for Electricity
Electric aviation’s success hinges on a robust electricity supply. Fortunately, the U.S. Department of Energy forecasts that renewable energy sources such as solar, wind, and hydro will account for a growing share of the national grid. With improvements in solar panel technology, wind farm capacity, potential new nuclear plant construction, and energy storage, the grid is likely to become both more powerful and more resilient.
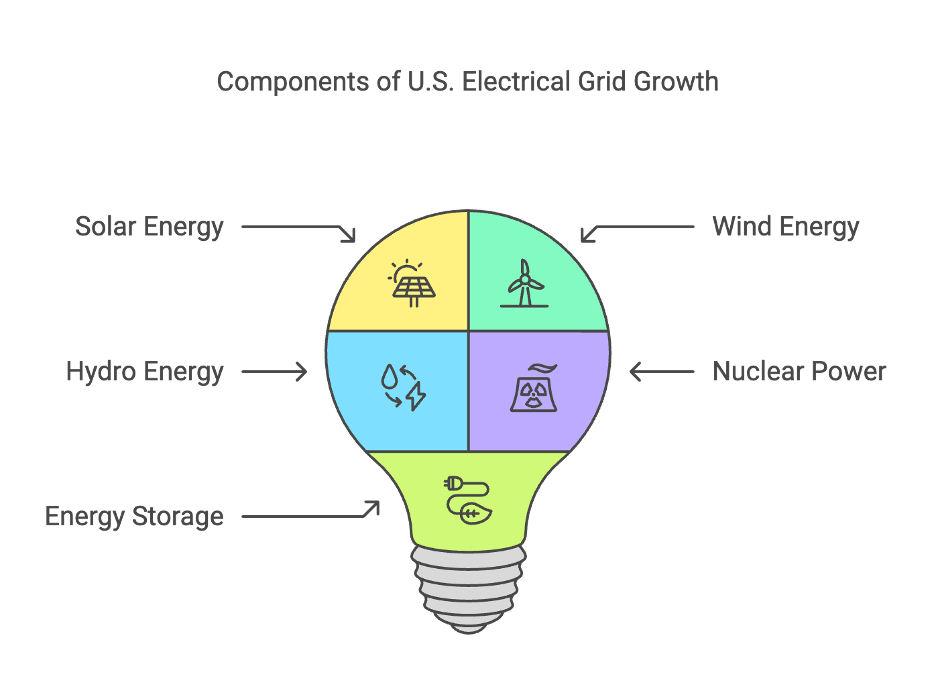
Impact of Charging Infrastructure
As the number of electric aircraft grows, airports and airline hubs will need to be retrofitted to include high-capacity charging stations. These systems will require specialized voltage and current outputs given the substantial energy needed to recharge an aircraft’s battery pack. Because large aircraft may need rapid charging solutions on tight turnarounds, the grid must be capable of delivering hundreds of kilowatts—sometimes over a megawatt—of power per charging session.
In the next ten years, we can expect federal or state-level incentives to expand the charging infrastructure at major airports, akin to how electric vehicle charging stations have proliferated. Private investments will also propel this expansion, especially as airlines form partnerships with energy providers. This demand, in turn, acts as a driver for improvements in the power grid overall, as it must keep pace with aviation’s electricity needs.
Alternative Means of Generating Electricity Onboard
While ground-based electrical charging will be the primary source of energy for many future aircraft, there is also significant research into onboard power generation technologies. These systems may serve as complementary or backup solutions, ensuring that aircraft remain operational even if ground infrastructure is unavailable or insufficient.
Hydrogen Fuel Cells
Hydrogen fuel cells are an appealing option for electric propulsion because they convert hydrogen gas directly into electricity, producing only water vapor as a byproduct. When integrated with battery packs, a fuel cell can act as a range extender—providing continuous power for longer flights while the battery handles peak loads. Although challenges remain in hydrogen production, storage, and handling, efforts are underway to create lighter, safer storage systems and “green hydrogen” production methods (e.g., electrolysis powered by renewable energy).
Turbine Generators
Another method for generating onboard electricity involves small gas turbines or turboshaft engines that drive electric generators. These hybrid-electric systems reduce total fuel consumption by allowing the turbine to run at optimal efficiencies while the battery provides supplementary power. Although this system does not eliminate emissions, it can significantly lower them compared to traditional propulsion.
Solar-Integrated Designs
Some concept aircraft feature solar panels integrated into the wings and fuselage to harvest energy from the sun. While the power gathered from solar panels alone is insufficient to propel a large passenger aircraft, it can power onboard systems or provide supplementary battery charging. Over the next decade, advances in flexible solar cells and aerodynamic designs could make solar integration a marginal but valuable source of extra energy.
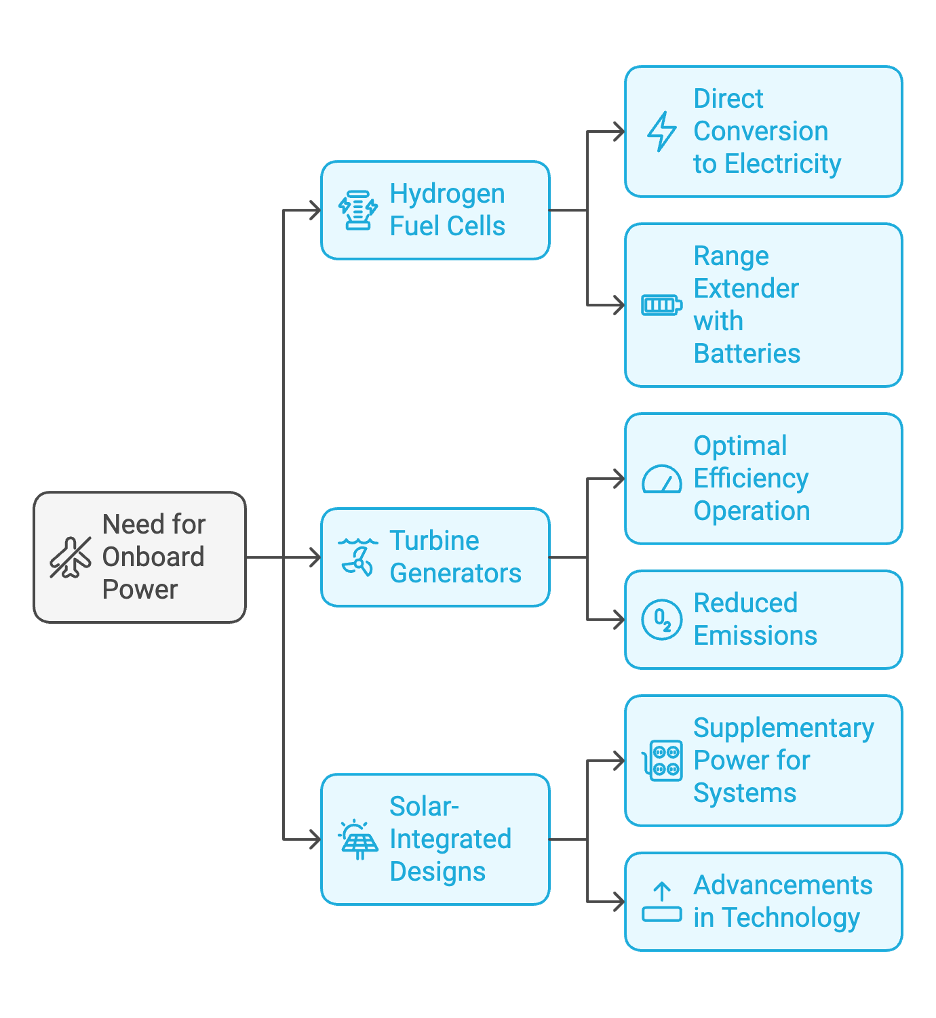
Stages of Adoption in Commercial Aviation
The transition toward electric aviation will not happen overnight. Rather, it will occur in phases characterized by incremental progress in battery capacity, aircraft range, and regulatory acceptance. Below are the likely stages:
- Stage One: Small Regional and Commuter Aircraft (2024–2027)
- Early electric propulsion systems will be deployed in small, short-range aircraft carrying fewer than 20 passengers.
- Aircraft of this size can be powered by current lithium-ion batteries with moderate energy densities (~300 Wh/kg).
- Airlines operating short routes (less than 200 miles) or serving remote communities will likely adopt these aircraft first to reduce costs and emissions.
- Stage Two: Scaling Up for Regional Airlines (2027–2030)
- By this time, battery technology—potentially solid-state or advanced Li-ion—may offer energy densities close to 400 Wh/kg, extending range capabilities up to 400 or 500 miles.
- Medium-sized aircraft (20-50 passengers) can then enter commercial service.
- Infrastructure expansion will accelerate, as airports begin installing high-capacity charging systems to support a growing electric fleet.
- Stage Three: Hybrid-Electric and Full-Electric Narrow-Body Aircraft (2030–2032)
- Major manufacturers will develop narrow-body aircraft (similar to the Boeing 737 or Airbus A320 families) with either hybrid-electric or fully electric powertrains.
- Ongoing AI-driven design innovations and new battery chemistries (e.g., lithium-sulfur) could lift energy densities to 500 Wh/kg or beyond.
- Flights of up to 600 or 700 miles become feasible, allowing a substantial portion of short-haul routes to go electric.
- Stage Four: Widespread Adoption for Short- to Medium-Range Routes (2032–2034)
- By the early 2030s, airlines will begin phasing in electric and hybrid-electric aircraft for a majority of regional and short-to-medium-haul routes—those under approximately 1,000 miles.
- Hydrogen-powered fuel cells or onboard turbine generators may appear as range extenders in more advanced designs.
- The aviation sector experiences notable reductions in carbon emissions, supported by a rapidly growing charging infrastructure and stable battery supply chains.
Illustrations of Key Concepts
Below are some conceptual illustrations to help visualize the shift toward electric aviation:
- Basic Electric Aircraft Architecture
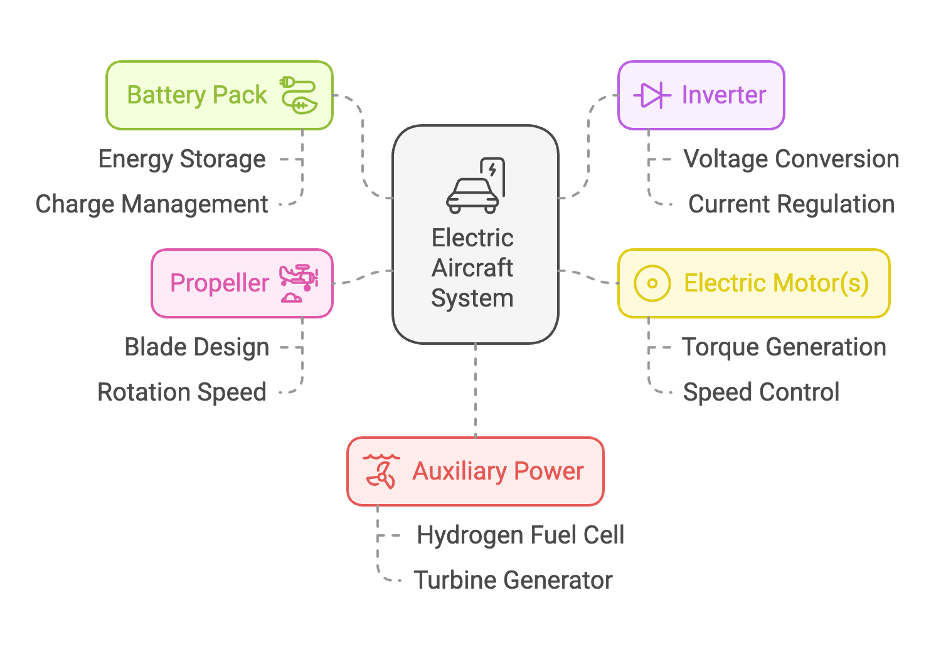
- Projected Increase in Battery Energy Density
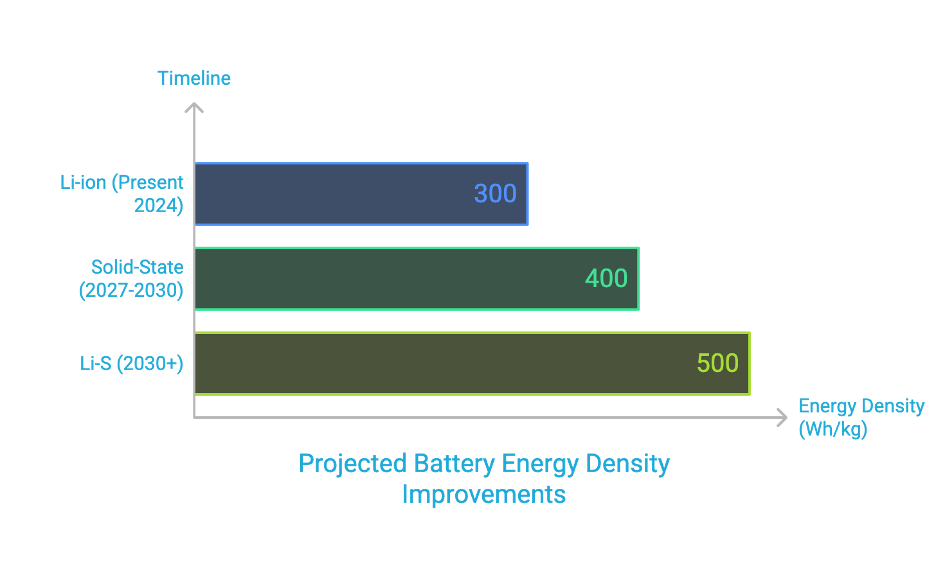
- Stages of Electric Aviation Adoption
Figure 3: A timeline concept showing how electric aviation might progress from small commuter aircraft to larger models with extended range.
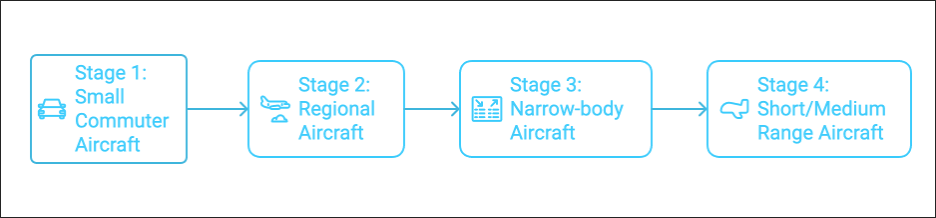
Key Challenges and Considerations
Despite the optimistic outlook, several challenges must be addressed:
- Weight and Range Trade-Offs: Batteries remain heavier than conventional fuel. Carrying more batteries increases aircraft weight, reducing range and payload capacity. This necessitates continual advancements in energy density and weight reduction.
- Charging Time: Fast-charging a large aircraft battery demands extremely high power levels. Airports must be able to deliver these power levels without disrupting local grids. Battery cooling and system safety also require careful management.
- Infrastructure Costs: Retrofitting existing airports with electric infrastructure is costly and complex. Power lines, transformers, and large-scale charging stations all need to be installed and certified for aviation use.
- Regulatory Hurdles: Aviation safety standards are strict, and new electric propulsion systems will require careful certification processes. Regulatory bodies like the FAA (Federal Aviation Administration) and EASA (European Union Aviation Safety Agency) need to develop updated guidelines.
- Economic Feasibility: Even as battery prices drop, airlines must ensure that electric aircraft bring a compelling return on investment (ROI). If operational savings (e.g., lower fuel costs, less maintenance) are offset by high up-front costs, adoption could slow.

Commercial aviation stands on the threshold of a major transformation, driven by both environmental imperatives and technological breakthroughs. In the coming decade, we can expect to see a steady rollout of electric and hybrid-electric aircraft, beginning with small commuter planes and eventually scaling up to larger regional jets. The evolution of battery chemistry—from current lithium-ion to solid-state and beyond—will play a pivotal role in achieving greater flight ranges and improved operational feasibility. Meanwhile, hydrogen fuel cells, onboard turbine generators, and even solar integration will provide alternative ways to generate or supplement power onboard.
AI design tools will help accelerate this transition by optimizing aircraft architectures, reducing prototyping times, and identifying new methods for integrating lightweight materials. At the same time, developments in the U.S. electrical grid—particularly the growth of renewables—will support a future in which electric aviation can plug into a robust, clean energy source. As airlines, manufacturers, and regulators unite to address infrastructure and certification challenges, the stage is set for a significant reduction in the carbon footprint of air travel by 2034.
Ultimately, the move to electric flight will be neither instant nor without obstacles, but the convergence of rising environmental demands, regulatory constraints, technological innovation, and public desire for clean travel strongly suggests that electric commercial aviation is more than a futuristic idea—it is an imminent reality. By embracing advanced battery technology, AI-driven design, and greener power generation methods, the aviation sector can make meaningful strides toward sustainability while maintaining the speed, safety, and global connectivity that have become hallmarks of air travel.